Shrinking & Settling
When timber is harvested for log home construction (with the exception of standing dead timber), the wood is typically near its “fiber saturation point,” or 30 percent moisture content. From the moment a tree is cut, it will begin to lose moisture and slowly and subtly shrink. For about a year after the logs are constructed as part of a home, they will continue to shrink until the logs reach what’s called “equilibrium moisture content” and acclimate to the surrounding environment (typically 8 to 12 percent moisture content).
When a system of logs is stacked to make a wall, the entire stack will shrink as the logs dry. This process is called settling and is completely natural to log home construction. Log home manufacturers (the companies that sell log home packages) design and engineer their homes to account for settling. Some companies will kiln dry their logs to near the equilibrium moisture content prior to construction to minimize settling. Others will use flexible joining products to accommodate the shrinking logs throughout the home.
Because there are numerous accepted methods of accounting for shrinkage, if you’re a home buyer planning to have a log home built, you’ll will want to discuss the issuesof shrinkage and settling with the manufacturer prior to building.
When timber is harvested for log home construction (with the exception of standing dead timber), the wood is typically near its “fiber saturation point,” or 30 percent moisture content. From the moment a tree is cut, it will begin to lose moisture and slowly and subtly shrink. For about a year after the logs are constructed as part of a home, they will continue to shrink until the logs reach what’s called “equilibrium moisture content” and acclimate to the surrounding environment (typically 8 to 12 percent moisture content).
When a system of logs is stacked to make a wall, the entire stack will shrink as the logs dry. This process is called settling and is completely natural to log home construction. Log home manufacturers (the companies that sell log home packages) design and engineer their homes to account for settling. Some companies will kiln dry their logs to near the equilibrium moisture content prior to construction to minimize settling. Others will use flexible joining products to accommodate the shrinking logs throughout the home.
Because there are numerous accepted methods of accounting for shrinkage, if you’re a home buyer planning to have a log home built, you’ll will want to discuss the issuesof shrinkage and settling with the manufacturer prior to building.
Cracks & Checks
Knowing that the shrinkage of logs in your new home is not a worry, what about cracks in the logs? You will likely notice small horizontal cracks in your home’s logs, but is that cause for concern?
In log homes, these cracks are called checks and they shouldn’t be a source of great concern. Checks are naturally occurring lengthwise separations between wood fibers. As your logs dry – moving from fiber saturation point to equilibrium moisture content – it is natural that checks will appear. In fact, if you look at the logs used in most model and show homes, you will notice these checks yourself. The trap that Mark Feder’s customer fell into was that she was so enamored with a model home’s interior decoration and design, she failed to notice the natural checks in the home’s walls. In properly graded logs, checking is typically a non-issue.
If your home has an upward-facing check on an exterior log, however, excess water can collect in the fissure and cause damage. Your home’s manufacturer will have a specific method of dealing with this issue, as it is common. It may take a simple sealant or caulk to fill the check, but always consult your manufacturer prior to attempting to fill the check.
Knowing that the shrinkage of logs in your new home is not a worry, what about cracks in the logs? You will likely notice small horizontal cracks in your home’s logs, but is that cause for concern?
In log homes, these cracks are called checks and they shouldn’t be a source of great concern. Checks are naturally occurring lengthwise separations between wood fibers. As your logs dry – moving from fiber saturation point to equilibrium moisture content – it is natural that checks will appear. In fact, if you look at the logs used in most model and show homes, you will notice these checks yourself. The trap that Mark Feder’s customer fell into was that she was so enamored with a model home’s interior decoration and design, she failed to notice the natural checks in the home’s walls. In properly graded logs, checking is typically a non-issue.
If your home has an upward-facing check on an exterior log, however, excess water can collect in the fissure and cause damage. Your home’s manufacturer will have a specific method of dealing with this issue, as it is common. It may take a simple sealant or caulk to fill the check, but always consult your manufacturer prior to attempting to fill the check.
The “Natural” Look
Today’s log home and coating manufacturers offer their products in a variety of colors. Some homeowners, however, want to preserve the natural color of their log home. If you fall into this group, don’t think that you can keep your home’s natural hue without applying any coating or sealant to the exterior.
Over time, as your home’s logs dry and are exposed to the sun, your wood’s beautiful natural color will slowly turn an unmistakable shade of gray. While this is wood’s natural reaction to dryness and sunlight, it catches many homeowners off guard. Should you wish to retain the natural color of your home, there are many sealants and coatings available that are colorless and will properly preserve color and its structural integrity. Your manufacturer may recommend a particular sealant or coating to use with its logs. Be sure to read the sealant or coating manufacturer’s instructions carefully and, if necessary, speak with a company representative to learn proper application techniques.
The unique beauty and tranquility of log home living are difficult to put into words. But the practical considerations and properties unique to a log home aren’t any more intensive than what is required in a conventional home; they’re just different. As long as you understand your log home’s unique properties, there is no reason you cannot enjoy your log home for decades – without worries about shrinking, cracking or turning gray.
Eric Fulton, communications manager for the Building Systems Councils of the National Association of Home Builders, says it’s vital that log home buyers seek out manufacturers with a clear construction manual and reputable building practices.
Today’s log home and coating manufacturers offer their products in a variety of colors. Some homeowners, however, want to preserve the natural color of their log home. If you fall into this group, don’t think that you can keep your home’s natural hue without applying any coating or sealant to the exterior.
Over time, as your home’s logs dry and are exposed to the sun, your wood’s beautiful natural color will slowly turn an unmistakable shade of gray. While this is wood’s natural reaction to dryness and sunlight, it catches many homeowners off guard. Should you wish to retain the natural color of your home, there are many sealants and coatings available that are colorless and will properly preserve color and its structural integrity. Your manufacturer may recommend a particular sealant or coating to use with its logs. Be sure to read the sealant or coating manufacturer’s instructions carefully and, if necessary, speak with a company representative to learn proper application techniques.
The unique beauty and tranquility of log home living are difficult to put into words. But the practical considerations and properties unique to a log home aren’t any more intensive than what is required in a conventional home; they’re just different. As long as you understand your log home’s unique properties, there is no reason you cannot enjoy your log home for decades – without worries about shrinking, cracking or turning gray.
Eric Fulton, communications manager for the Building Systems Councils of the National Association of Home Builders, says it’s vital that log home buyers seek out manufacturers with a clear construction manual and reputable building practices.
LOG HOME MYTHS
Still considered a niche industry, log homes are subject to more myths than other types of construction. The Log Homes Council sets the record straight.
Myth: There is one ideal type of wood used in log homes.
Reality: Dozens of species of wood are used in log homes. While natural properties of wood vary by species, the complete log home system (including sealants, chinking, etc.) ensures that all log homes enjoy the same qualities of thermal efficiency, insect resistance and overall beauty.
Myth: Log homes are difficult to build – even for experienced builders.
Reality: Building a log home is not complicated; it is just different for some experienced builders who typically build other types of homes. Log home manufacturers acknowledge this and many provide a construction manual for their log system and routinely hold introductory courses for interested builders.
Myth: Log homes are limited in design and function.
Reality: Maybe true 40 years ago, but today’s log homes benefit from computer-assisted design and modern engineering. Nearly any architectural style or flourish is possible.
Myth: Log homes are difficult to finance and insure.
Reality: Several leading banks, mortgage companies and insurance agencies now specialize in log homes. You can find these companies online, at log home shows and even in your local phone book.
Myth: Log homes need a large amount of maintenance.
Reality: Maintaining a log home requires no more effort than a conventional home, just a different type of maintenance. Be sure to perform an annual check-up on your log home and consult with your manufacturer about the proper care and preservation required.
– Eric Fulton
Still considered a niche industry, log homes are subject to more myths than other types of construction. The Log Homes Council sets the record straight.
Myth: There is one ideal type of wood used in log homes.
Reality: Dozens of species of wood are used in log homes. While natural properties of wood vary by species, the complete log home system (including sealants, chinking, etc.) ensures that all log homes enjoy the same qualities of thermal efficiency, insect resistance and overall beauty.
Myth: Log homes are difficult to build – even for experienced builders.
Reality: Building a log home is not complicated; it is just different for some experienced builders who typically build other types of homes. Log home manufacturers acknowledge this and many provide a construction manual for their log system and routinely hold introductory courses for interested builders.
Myth: Log homes are limited in design and function.
Reality: Maybe true 40 years ago, but today’s log homes benefit from computer-assisted design and modern engineering. Nearly any architectural style or flourish is possible.
Myth: Log homes are difficult to finance and insure.
Reality: Several leading banks, mortgage companies and insurance agencies now specialize in log homes. You can find these companies online, at log home shows and even in your local phone book.
Myth: Log homes need a large amount of maintenance.
Reality: Maintaining a log home requires no more effort than a conventional home, just a different type of maintenance. Be sure to perform an annual check-up on your log home and consult with your manufacturer about the proper care and preservation required.
– Eric Fulton
Mark Feder still remembers picking up the phone and hearing a woman sobbing on the other end. She had called Mark to discuss her problem and ended the call questioning the decision she had made. Is this a story of a spurned lover?
Hardly.
Mark Feder is vice president of sales for Appalachian Log Structures and past president of the Log Homes Council, and on the other end of his telephone line was a customer convinced her log home was falling apart.
For all her research of log homes prior to purchasing her own, Mark’s customer never noticed the small, natural cracks – called checks – that occur in log walls. Having spied some checks in her home, she was convinced her home was in danger of crumbling to pieces. Mark’s customer was quickly relieved to learn that these checks were common to all log homes and that her home was structurally sound.
However, she found out the hard way that when it comes to purchasing and living in a log home, no amount of knowledge is too much.
It can come as a shock to learn that in the first few years after a log home is built, it has an innate desire to turn gray and stands a good chance of shrinking and cracking. But educated home buyers will know that building with logs – a 100 percent natural product – has many advantages, and any pitfalls related to solid-wall log construction are easily accounted for and can be avoided.
Hardly.
Mark Feder is vice president of sales for Appalachian Log Structures and past president of the Log Homes Council, and on the other end of his telephone line was a customer convinced her log home was falling apart.
For all her research of log homes prior to purchasing her own, Mark’s customer never noticed the small, natural cracks – called checks – that occur in log walls. Having spied some checks in her home, she was convinced her home was in danger of crumbling to pieces. Mark’s customer was quickly relieved to learn that these checks were common to all log homes and that her home was structurally sound.
However, she found out the hard way that when it comes to purchasing and living in a log home, no amount of knowledge is too much.
It can come as a shock to learn that in the first few years after a log home is built, it has an innate desire to turn gray and stands a good chance of shrinking and cracking. But educated home buyers will know that building with logs – a 100 percent natural product – has many advantages, and any pitfalls related to solid-wall log construction are easily accounted for and can be avoided.
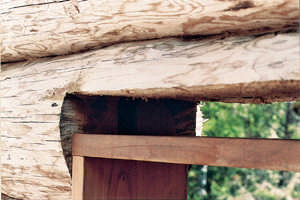
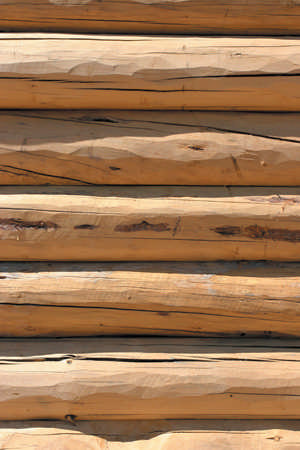
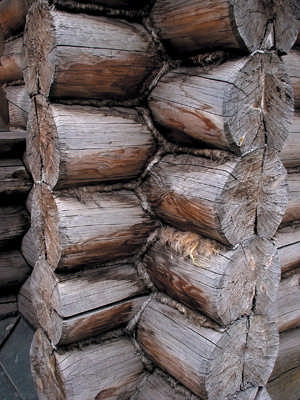
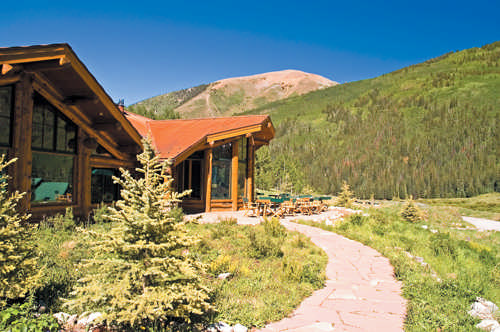