When it comes to adding a garage or storage space at the cabin, you need a building that’s low-maintenance, able to withstand the elements and big enough to accommodate vehicles, ATVs, boats and all the other tools and toys that go hand-in-hand with cabin living. Sounds like a job of superhero proportions.
A steel garage with post-frame construction is inherently strong and offers large open spaces. And with prices for steel and structural lumber on a downswing, a steel garage also can be an affordable, practical sidekick for your cabin. Add in low-interest rates and competitive pricing for turnkey garages – especially for structures erected by a professional crew during the winter months – and it’s no wonder steel garages are popping up on cabin properties all over the country.
The real advantages of steel are most evident in a post-frame building, sometimes called a pole barn. While originally designed for agricultural purposes, the widely spaced poles (actually laminated 6x6-inch posts) and trusses allow a floor plan with wider spans than those with traditional stick-built garages. Add in a wide variety of colors and an overhanging eve design, and nobody will ever suspect your post-frame garage’s ancestors were responsible for keeping rain off of Uncle Fred’s hay baler.
The quality that Uncle Fred liked most about his pole barn of yesteryear is still true in today’s steel garage: the ability to go large. Post-frames can run over 100 feet in length, though the size of the typical cabin storage space is more like 30x40 feet.
Going smaller isn’t a problem, of course … though the lament of “I made my garage too darn big” is pretty rare.
While it can be fairly difficult to build a large post-frame building by yourself, most suppliers have crews that can put up even a huge garage in a day or two.
Given the advantages and popularity of post-frames, it isn’t too surprising that there are myriad manufacturers from which to choose. Here are some tips for choosing the best one for your money:
A steel garage with post-frame construction is inherently strong and offers large open spaces. And with prices for steel and structural lumber on a downswing, a steel garage also can be an affordable, practical sidekick for your cabin. Add in low-interest rates and competitive pricing for turnkey garages – especially for structures erected by a professional crew during the winter months – and it’s no wonder steel garages are popping up on cabin properties all over the country.
The real advantages of steel are most evident in a post-frame building, sometimes called a pole barn. While originally designed for agricultural purposes, the widely spaced poles (actually laminated 6x6-inch posts) and trusses allow a floor plan with wider spans than those with traditional stick-built garages. Add in a wide variety of colors and an overhanging eve design, and nobody will ever suspect your post-frame garage’s ancestors were responsible for keeping rain off of Uncle Fred’s hay baler.
The quality that Uncle Fred liked most about his pole barn of yesteryear is still true in today’s steel garage: the ability to go large. Post-frames can run over 100 feet in length, though the size of the typical cabin storage space is more like 30x40 feet.
Going smaller isn’t a problem, of course … though the lament of “I made my garage too darn big” is pretty rare.
While it can be fairly difficult to build a large post-frame building by yourself, most suppliers have crews that can put up even a huge garage in a day or two.
Given the advantages and popularity of post-frames, it isn’t too surprising that there are myriad manufacturers from which to choose. Here are some tips for choosing the best one for your money:
1. Get the right garage for your location. Ask any prospective bidder if his/her garage designs are tailored for the geographic area. Weather conditions, from snow load to hail potential, should be reflected in the garage’s design (which should also have an engineer’s stamp affixed).
2. Consider the type of steel. While every post-frame builder will have his/her own steel, the gauge (thickness) and grade (tensile strength) follow standard codes. The lower the gauge, the thicker the metal. When it comes to tensile strength, a structural grade will have up to a 30,000 additional p.s.i. (pound force per square inch) rating when compared to commercial grade.
2. Consider the type of steel. While every post-frame builder will have his/her own steel, the gauge (thickness) and grade (tensile strength) follow standard codes. The lower the gauge, the thicker the metal. When it comes to tensile strength, a structural grade will have up to a 30,000 additional p.s.i. (pound force per square inch) rating when compared to commercial grade.
3. Who’s building this thing? Does the manufacturer employ its own crew, with detailed knowledge of those particular post-frame materials? Is the construction crew coming in from out-of-state, or are they local tradesmen with a vested interest in the community? Do they have workers’ compensation insurance? No matter how good the materials or how well it’s engineered, a post-frame is only as good as the people who build it.
4. Get the “all-in” estimate. Doors, windows and trim can add significant out-of-pocket costs to your project. Also, ask what kind of overhang the building has, if any; overhanging eaves add character, charm … and cost. If the details are not clear, ask for a detailed cost estimate showing exactly what is included in the quote.
4. Get the “all-in” estimate. Doors, windows and trim can add significant out-of-pocket costs to your project. Also, ask what kind of overhang the building has, if any; overhanging eaves add character, charm … and cost. If the details are not clear, ask for a detailed cost estimate showing exactly what is included in the quote.
5. How well do they stand behind their product? Most manufacturers will throw out 25-year warranties on their steel like firemen tossing out candy at the Fourth of July parade. But ask if the warranty covers the posts or workmanship. And avoid pro-rated warranties if possible; every year your warranty loses some of its power.
6. Do they offer a winter discount? Since post-frames don’t need to be placed on a concrete slab, you can build right through the winter months and save a few bucks in the process. You’ll need to level your building site and probably add some gravel for a base before freeze-up. Most people simply use the bottom bracing on the posts as the frame for the slab, which can be poured when things warm back up.
Once you’ve got a potential builder, see if you can talk to a previous customer or two and even take a look at his/her garage. If things still look good, you’re well on your way toward choosing a garage that can stand up to just about anything … kryptonite included.
Kurt Anderson, the proud owner of a two-and-a-half-car garage, still suffers from occasional bouts of garage envy. He swears his next garage will be visible from space.
6. Do they offer a winter discount? Since post-frames don’t need to be placed on a concrete slab, you can build right through the winter months and save a few bucks in the process. You’ll need to level your building site and probably add some gravel for a base before freeze-up. Most people simply use the bottom bracing on the posts as the frame for the slab, which can be poured when things warm back up.
Once you’ve got a potential builder, see if you can talk to a previous customer or two and even take a look at his/her garage. If things still look good, you’re well on your way toward choosing a garage that can stand up to just about anything … kryptonite included.
Kurt Anderson, the proud owner of a two-and-a-half-car garage, still suffers from occasional bouts of garage envy. He swears his next garage will be visible from space.
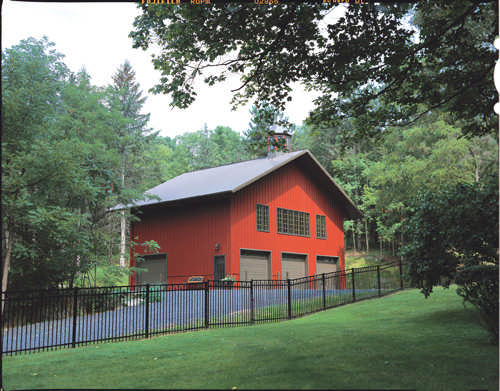

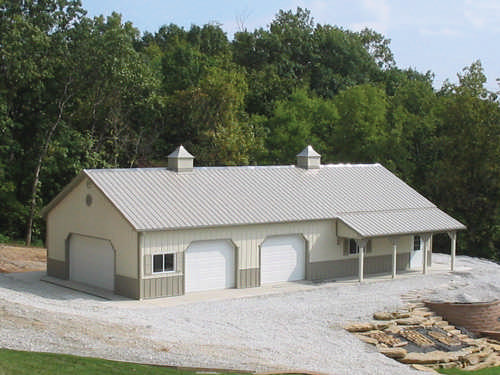
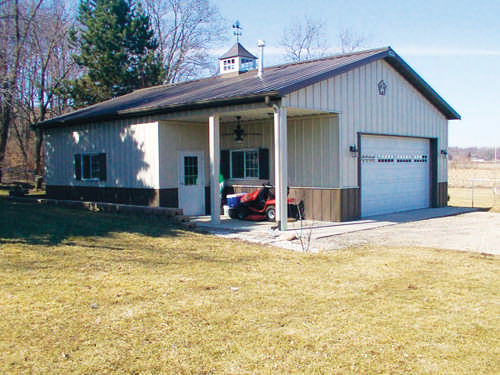