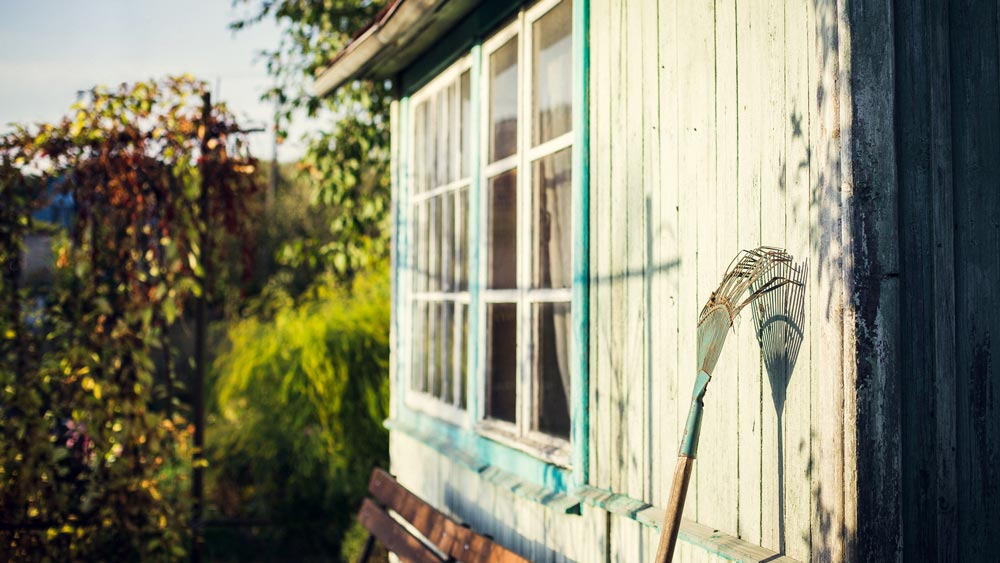
By Jim Cooper
Maybe a casual interest in gardening, woodworking or pottery has blossomed into a full-blown passion. Perhaps you’ve added a boat, four-wheelers, RV or started to collect antique tractors. Whatever the cause, your cabin lifestyle has exceeded its floorspace.
Either for storage or hobby, you need more space, and an outbuilding seems like the best solution. There are several paths to follow based on your needs and budget.
If you are simply looking for a place to store a mower or lawn tractor and some gardening tools, a small shed may be the answer. Most of the big box building suppliers offer a range of small sheds that can be purchased as kits or fully assembled buildings that can be trailered to your site. Usually these range in size from 8x8 feet to approximately 16x24 feet. Costs range from less than a thousand dollars to over $10,000. Such mini-barns are usually conventionally framed using 2x4s and typical carpentry tools and techniques.
If you aren’t handy or otherwise not interested in a construction project, many areas have a small cottage industry of shed builders that can provide you with turnkey service. You’ll often find displays or even ready-to-deliver structures in local farmyards and parking lots. If you can’t seem to find someone, stop in a local feed, building or agricultural supply store and ask. They’ll almost certainly provide a few names.
If your needs point to a larger or more durable building, consider turning to the traditional staple of country outbuilding: the pole barn. Pole building is an inexpensive way to create durable structures ranging from small sheds to aircraft hangers. Calling them barns is somewhat unfair since pole structures include commercial buildings, manufacturing facilities retail centers, churches and even residences. You have probably driven past many pole buildings without even knowing it.
Unlike more lumber-intensive conventional framing, pole buildings rely on vertical posts joined by horizontal lumber girts. Posts are usually 6 to 8 inches square and spaced 6 to 8 feet apart. They are connected using horizontal 2x girts spaced at 2-foot intervals. Horizontal beams at the top of the posts support roof trusses. Since pole construction eliminates the need for interior posts or bearing walls, the entire interior can be free of inside posts or walls.
Pole buildings excel at providing large open interiors at reasonable cost. Pole construction offers several other unique advantages. Since pole buildings use less lumber, they typically cost less than conventional frame construction. Less framing lumber also means more room for insulation if needed. The absence of load-bearing walls eliminates the need for continuous footings and structural slabs, which saves money and allows more flexibility in size and placement of windows and doors. If a gravel floor is sufficient for your needs, you can eliminate thousands of dollars in concrete cost. Pole buildings are often sided and roofed with metal, creating a long-lasting, attractive structure.
Many providers offer both kit and turnkey alternatives. For turnkey, make sure the provider sees the site before providing a price. They may point out costs you hadn’t anticipated, such as additional clearing, drainage modification or soil adjustments that could otherwise be hidden extra costs. Pricing for kit or turnkey buildings should include engineering that ensures the building can accommodate snow and wind loads and meet all local codes.
Questions to Ask Before You Construct a Storage Building
- How much space do you need?
- What is your budget?
- Is your building site flat and accessible, or will you have to grade and/or clear? Flat sites are much easier and less expensive to build on.
- Will you erect the building yourself or hire a contractor? If you will be doing all or some of the construction, do you have the tools and experience?
- Are there local building codes? What are code requirements for the type of construction and use you are planning? Be especially careful to check footing and frost protection requirements.
- Will you need a concrete floor, or will gravel be sufficient?
- Will you need to insulate?
- What systems do you anticipate needing? Plumbing? Electrical? HVAC?
Resources
- Morton Buildings –A nationwide network of design-builders, Morton can accommodate projects of any size, residential or commercial.
- Wick Buildings – The company provides a materials package including design and engineering, then works with a network of local builders for construction services. Wick can also provide building packages to be erected by your builder. Serves the Midwest, Great Lakes and Great Plains.
- Hansen Buildings – Providing materials packages that include stamped engineering drawings, Hansen offers both pre-configured kits and custom design services. Located in Minnesota but ships nationwide.
- APB Pole Barns– Located in Texas, APB offers nationwide turnkey services or kits. Engineer-stamped drawing fees, if required, are extra.