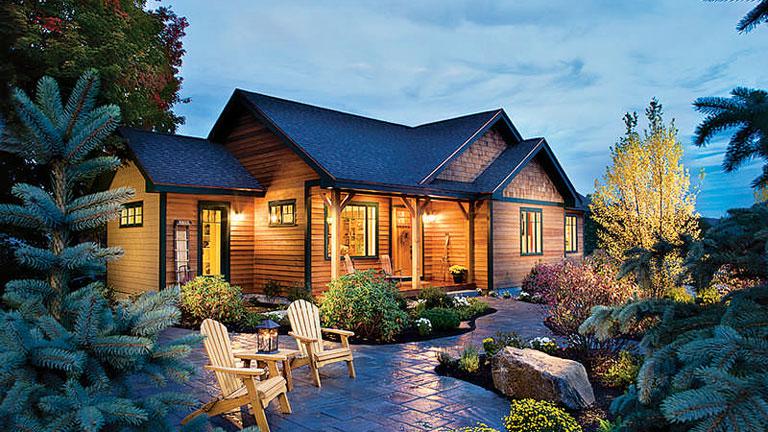
When you hear the word “cabin,” what’s the first thing that pops into your head? A log home in the mountains? A cozy lakeside cottage? A tiny house in the woods? Something completely different? The image you conjured up can help you determine your cabin style; it also helps to know your construction options, so that you can go from figments of imagination to a retreat home in the real world. Begin by familiarizing yourself with construction types commonly used for cabins. In the end, you will probably choose to go with a log, timber-frame, stick-built or modular home.

How Much Does a Cabin Cost?
As you research your options, be aware that you may run across cost-per-square-foot comparisons. These shorthand estimates may seem helpful but in the long run can prove meaningless. “Some costs are constant regardless of the size of home – permits, environmental and other government fees, inspections and utility hook-ups are unaffected by a home’s size,” says Paul Foresman of Design Basics LLC, a home plan company based in Omaha, Neb. “A smaller home will still have a kitchen sink, dishwasher, range, refrigerator and microwave – just like a larger house,” Foresman says.
In general, the cost-per-square-foot for a small cabin will be higher than for a larger home, simply because the fixed costs are divided by fewer square feet. If you’re trying to contain costs, keep your plan simple. “That old adage, ‘corners cost,’ is important whatever size your home might be,” says Bonnie Pickartz of Goshen Timber Frames of Franklin, N.C. “Simplifying the foundation will simplify the roof line, saving money from the ground up. Discussing what design issues, finishes and styles are important is critical to maintaining the budget and keeping costs in line.”

Building a Log Cabin
For some people, log construction is synonymous with cabins. If you plan to build with logs, you’ll have choices to make within that category:
Handcrafted Logs
These create a home with a more organic feel. Handcrafted logs are carved to stack on top of each other in exterior walls. For a more historic look, some handcrafters hew logs into rectangular profiles with flat exterior and interior faces. In general, handcrafted log homes use larger logs than milled log homes and come with a higher price tag.
Milled Logs
This type of logsare precision-cut to a uniform look and size. These logs come in a variety of profiles, from fully round to squared, to create the log cabin look you prefer. Some log home producers offer “super-insulated” exterior walls, created by using dimensional log siding on the interior and exterior of stud-framed and insulated walls. This option gives the look of a full log wall with added energy efficiency.
Log Siding
This approach works for people who want the look of logs and are either renovating an existing cabin or building something new. Log siding can be applied to a cabin’s exterior walls only or added to the interior walls, as well. How is log siding created? Options include milling it from logs or manufacturing it from concrete. Because of its integral color and durable material, concrete log siding allows for the look of wood with very low maintenance.
Log Home Packages
These can be purchased directly from a producer or through a local dealer, who may also serve as a builder. “There are many variables to the price of a log home,” according to the International Log Builders’ Association. “The design, species, style, size, roof structure and finish materials are just a few of the many factors.” If you design a cabin from scratch or a stock plan, you can control many of these factors in order to keep a log cabin within your budget. The benefits of log construction include its unique aesthetics and its ability to take on a variety of styles from Early American to eclectic to classic Western ranch.
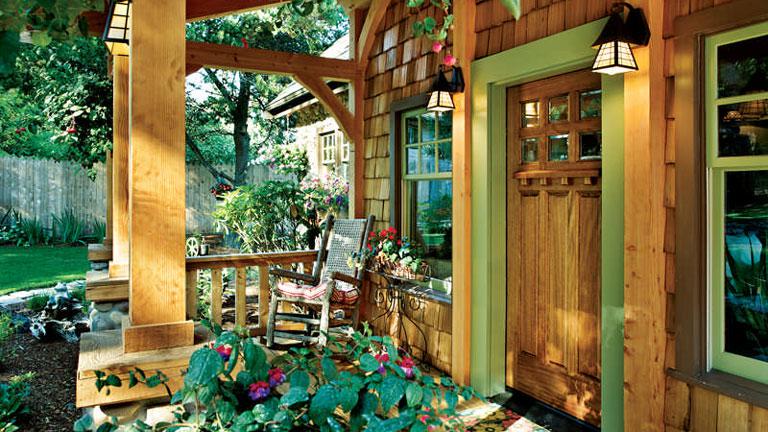
Timber Kings
Timber-frame or post-and-beam construction brings the beauty of wood to the interior of a cabin while allowing for wide-open spaces. Traditionally, timber frames are built using hand-carved wood joinery interlocked with wooden pegs. Post-and-beam construction may use timbers that are joined with metal plates or other hardware. An online search or a trip to a specialty home show can introduce you to timber framers in your area or across the country. You will work with a framer and a designer or architect to plan your cabin. Some framers will enclose the frame with exterior walls; others will simply cut and erect the frame, which will then be finished by your local builder.
Timber-framed cabins can rank high in “wow” factor. Soaring ceilings and the unique character of wood add to the charm of this construction type. A timber frame can be uniquely weathertight thanks to enclosure systems (like structural insulated panels, or SIPs) that wrap the frame in an envelope of insulation. A well-insulated home will save money year after year, Pickartz notes. A timber-frame or post-and-beam cabin can take on a wide variety of styles to suit any taste.
Weighing the cost of a timber frame to a stick-built home is only possible if you can truly compare apples to apples, Pickartz explains. “Given the same roof lines, finishes and square footage, there is very little difference in a custom stick-built home and a custom timber frame.” She cautions that if you like the beauty of wood, “a stick-frame home might need boxed beams, paneling and additional woodwork to give it that cabin feel, timber frames come to the party with these things as part of their structural design.”
Watching the budget? You can choose a hybrid home that features timbers only in certain areas (like a great room) or choose a local, readily available wood for your frame. Working with a designer to eliminate expensive, unused spaces will also help the bottom line.
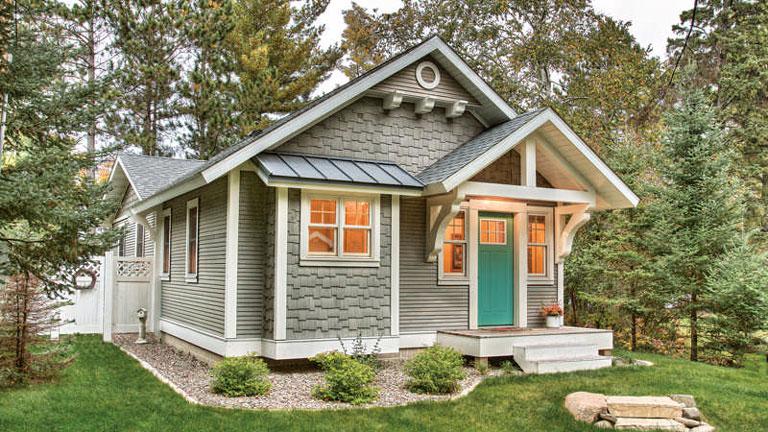
The Story on Stick-Built Cabins
Stick-built cabins have walls that are framed with conventional studs. Common in home building, stud-framed construction takes advantage of widely available building materials. If you plan to build a stick-framed cabin from scratch, you will rely on the services of a local builder or general contractor. That builder will work with the plan and list of specifications you supply to build your custom home. Because this type of construction is widely used, you should have your pick of contractors with experience.
A stick-built cabin can be created in any style – from shabby chic to farmhouse to mountain style to traditional. Plenty of stock floor plans are available for you to choose from, and they can be revised with help from a designer or architect.
This type of construction is also familiar to lenders and insurance companies, so you would have fewer hassles paying for and insuring this type of cabin. The cost of a custom cabin built using conventional construction will vary widely from region to region and will be affected by the level of finishes you choose and the complexity of your plan. “Your kitchen selections alone could increase your home’s overall cost by $10 to $20 per square foot or more,” Foresman of Design Basics says.
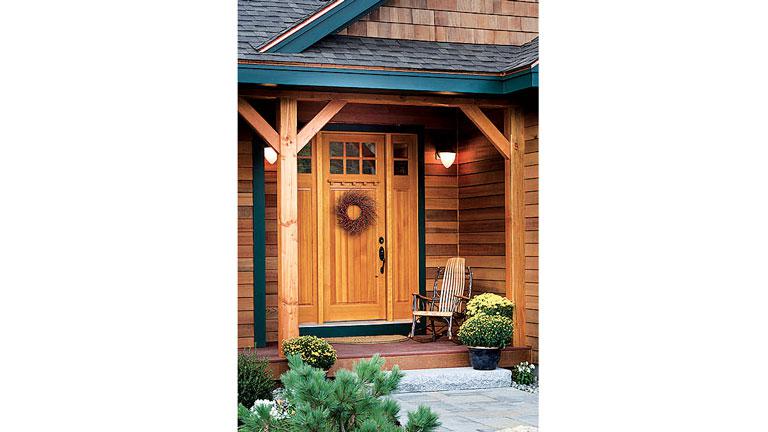
Modular Cabins
With its emphasis on a quality product and quick build times, modular construction has appeal for cabin lovers. Modular homes are built in sections (or modules) in a company’s indoor facility and then shipped to the construction site to be placed on a permanent foundation. Not to be confused with mobile or manufactured homes, modular homes are available in every size and style that can be created with conventional on-site construction.
Eliminating the variables of weather and material waste, modular construction can result in a cabin that meets or exceeds energy-efficiency standards, according to the Modular Home Building Council of the National Association of Home Builders. Costs can be similar to or somewhat less than conventional stud-framed construction, depending on the complexity of your modular home and where you plan to build.
As with other forms of construction, you can rein in costs by building small: Extra modules will increase shipping costs to your site. A modular cabin, like any other custom home, can be a place to take on do-it-yourself projects, but hiring a general contractor to oversee the site development, foundation build and finish work is typical for modular home buyers. For those building on a remote site or in a climate with a short building season, modular construction can be a good choice. “In some remote areas it’s very difficult to transport and house a construction team making it a headache for traditional site-built construction,” says Tim Key of Modular Today. As with timber framing, where a crane is used to set large timbers, the modular construction site needs to have enough clear space for crane access. “When building in a remote area, the roads are a concern for your delivery, but a bigger concern is ensuring there is enough room for the crane to lift and maneuver your modular,” Key explains.
To start your search for a modular cabin, look for a local builder who has experience with this type of construction. “Modular home-building experience is very important when picking your local builder,” Key says. “For example, foundations for modular homes often need to be much more precise than stick-built homes.”
The Bottom Line
All the planning and good faith estimating in the world won’t help you foresee every possible circumstance when building a cabin. No matter what type of construction method you choose, surprises can pop up. The experts at Modular World suggest reserving at least 5% of your budget (or more, if possible) as a contingency fund to pay for unexpected issues that arise as you build your dream cabin.